In early 2022 the Health and Safety Executive (HSE) completed a
project to update the evidence base on wood dust exposure risks in
British manufacturing industries. In so doing, HSE gained a better
understanding of how it could support small and medium-sized
woodworking enterprises in controlling exposure to wood dust.
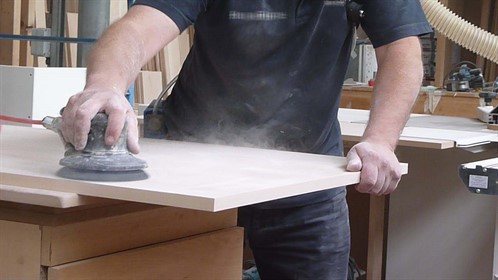
Airborne wood dust created during hand-held powered sanding
(© Crown Copyright, Health and Safety Executive)
The Challenge
There is a legal duty on employers to ensure that workplace
exposures do not exceed a given workplace exposure limit (WEL), to
follow good control practices and, for carcinogens and asthmagens,
to reduce exposure to as low a level as is reasonably practicable
(ALARP). Exposure to any wood dust can cause asthma and dermatitis,
whilst exposure to hardwood dust can also cause sino-nasal
cancer. At the time of this research, the WEL in Great
Britain for both softwood and hardwood dust was 5 mg/m³, based on
an 8-hour time weighted average (TWA). The limit for hardwood and
mixed hard and softwood dusts has since been reduced to 3 mg/m³ but
the WEL for softwood dust remains at 5 mg/m³. The Control of
Substances Hazardous to Health (COSHH) regulations remain
unchanged.
The Solution
Occupational hygiene assessment visits were carried out at
twenty-two woodworking manufacturing sites. The sites were selected
on the basis that they were believed to be following reasonably
good occupational hygiene control practice, enabling good practices
to be benchmarked. The sites visited covered furniture production,
joinery, saw milling and boat building. The sites were also invited
to participate in telephone interviews to gain a better
understanding of how HSE could support small and medium-sized
woodworking manufacturing enterprises in managing the control of
exposure to wood dust.
The Outcome
Overall 252 8-hour TWA wood dust exposure measurements were
obtained, of which 6% were greater than 5 mg/m³. Ten of the
twenty-two sites had at least one exposure greater than 5 mg/m³.
Out of the 216 exposures for sites which produced hardwood dust,
18% exceeded 3 mg/m³, the new WEL for hardwood (and mixed wood)
dusts.
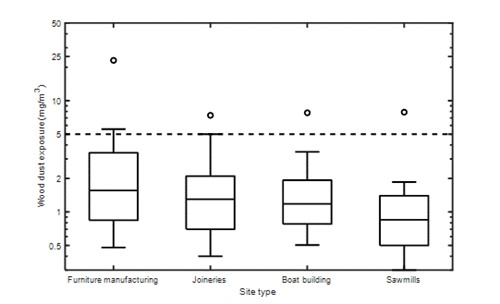
Figure 1 Wood dust exposure measurements by site type (8-hr
TWA)
The data are presented in a boxplot (Figure 1), where the circle
represents the highest exposure in that dataset, whiskers represent
the 10th and 90th percentiles, and the box represents the median
and 25th and 75th percentiles of the data. The dashed line
represents the WEL for hardwood and softwood dusts current at the
time of the survey. The sites were selected as good health and
safety performers, but exposures greater than the WEL were found in
all four sectors.
A number of task-based exposure measurements were also made for
cleaning and maintenance activities. Exposures for 3 out of 10
workers who were dry sweeping, and 5 out of 11 workers who were
changing waste sacks on dust extraction air cleaners, exceeded a
nominal 15 mg/m³ 15-minute short-term exposure limit (STEL). There
is no legal STEL for wood dust exposure, but a figure of three
times the long-term limit is recommended as a guideline for
controlling short-term peaks in exposure (EH40/2005 Workplace
exposure limits). For respiratory sensitisers such as wood dust,
activities giving rise to short duration peak concentrations are of
particular concern. Performing these short duration, high exposure
tasks made a disproportionately large contribution to the workers'
8-hour TWA exposures, significantly adding to their health
risk.
Dry sweeping is bad practice because it generates
high levels of airborne dust and should be
avoided.
Local exhaust ventilation (LEV) provision for fixed woodworking
machines was generally adequate to control wood dust exposures to
below 5 mg/m³, but was found to be poor for hand-held power tools
(e.g. orbital sanders and routers) and manual sanding. Most fixed
LEV systems underwent a 14-monthly thorough examination and test
(TExT), but most portable vacuum systems did not.
The management, selection and use of respiratory protective
equipment (RPE) was poor; the main issues were selection of
RPE with too low a standard of protection, lack of face fit testing
for tight-fitting RPE, and the incorrect use of RPE (e.g. use of
tight-fitting RPE with facial hair). Seventy-eight workers wore RPE
at some point, but only twenty-five were face fit tested and wore
it correctly.
Eight of the twenty-two sites had commissioned their own dust
monitoring survey and, although there was a reasonable likelihood
of health effects occurring in these sectors, only thirteen of the
sites had health surveillance in place.
Employers obtained information on how to control wood dust from
various sources. The most commonly mentioned source was the HSE website. They
recognised the health risks associated with exposure to wood dust
as well as the benefits of controlling wood dust, including
protecting workers' health, less time spent cleaning the workplace
and improved productivity. They also acknowledged a positive impact
on product quality. Approaches needed to raise awareness and
promote good practices among the workforce included challenging
poor practices and leading by example, as well as providing
information on the health effects of wood dust exposure and the
importance of controls. Challenges included worker attitudes toward
controls, poor habitual working practices, and limited availability
of resources for smaller companies.
In summary
- Many sites did not adequately control worker exposure to wood
dust. Employers are recommended to review their exposure
controls and implement any necessary improvements to comply with
the new WEL and meet the requirements set out in the COSHH
Regulations.
- Sanding was the activity that led to the highest long-term
exposures, whilst cleaning and maintenance tasks gave rise to high
short-term peak exposures which resulted in a disproportionate
effect on overall wood dust exposure. It is recommended that these
activities receive particular attention when managing the risks
from airborne wood dust.
- LEV performance was taken for granted on many sites and
daily/weekly maintenance checks were not carried out. Regular and
effective use of LEV with hand-held power tools was not observed.
Employers should ensure suitable LEV is both provided and used
effectively for fixed woodworking machines and for hand-held power
tools. LEV should be regularly checked and maintained for effective
performance and subjected to a TExT at least every 14 months.
- There was often a lack of knowledge about the management,
selection and use of RPE, and little training or supervision of
workers wearing RPE. Employers should ensure that the RPE chosen
offers adequate protection for the task, and is suitable for the
worker (e.g. face fitting is properly carried out for tight-fitting
RPE). They should also ensure that the RPE is used and maintained
correctly.
- Some sites lacked health surveillance for wood dust exposure.
On woodworking sites, where there is a reasonable likelihood that
workers could develop occupational asthma and/or dermatitis, a
health surveillance programme should be in place. This programme
should be set up by the employer in consultation with a competent
Occupational Health professional.
- Workers' engagement in healthy and safe working practices is
crucial. Employers might benefit from using risk communication
approaches that focus on increasing workers' awareness of their
susceptibility to ill health and encourage the use of controls.
Communication using credible sources, such as peers, may enhance
effective uptake of the message. Benefits relating to the control
of wood dust, such as improved productivity and product quality
could serve as a means of promoting good practice across the
industry.