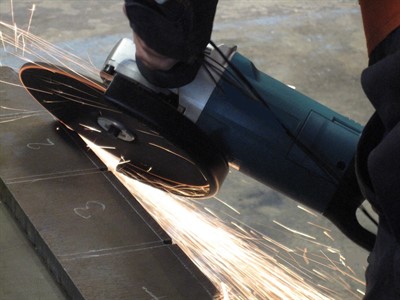
The Challenge
Hand-held angle grinders are widely used across many sectors,
including steel frame fabrication. Real-use measurements on angle
grinders show upper quartile values in the range 7 to 9 m/s², this
means that there is a risk of ill health to operators regularly
using these machines for as little as 20 minutes per day and a high
number of hand-arm vibration syndrome (HAVS) RIDDORs are
investigated from steel frame fabrication. Grinders also typically
produce LAeq noise levels of around 90 to 95 dB(A), making them a
significant contributor to occupational noise exposure.
In addition to hand-arm vibration (HAV) and noise, many
hand-held grinder users are also exposed to other physical hazards
such as dust. Methods used to control dust, such as masks and water
suppression systems, do not make any contribution to mitigating the
effects of HAV and noise or to reducing musculoskeletal
disorders.
The most effective way of controlling exposures from
grinders is to reduce or eliminate the use of these
machines.
This project investigated alternative processes to grinding as
well as methods designed to reduce emissions from grinders. We
tested a range of different abrasive wheels such as: standard
grinding wheels, flap discs, ceramic discs, fibre disc with a
rubber backing pad, diamond discs and carbon discs. In addition,
alternative tools were tested such as rebar cutters, bevelling
machines and an angle grinder with a built in autobalancer. The
tools and wheels were subjected to 3 different tests: grinding,
bevelling and cutting. Noise, vibration and dust measurements were
taken for each test.
The Solution
For all tasks there are alternatives that could reduce the
worker's exposure to vibration, noise and dust when compared to
standard wheels and angle grinders. In addition, there are machines
available that may produce higher levels of vibration, but
significantly reduce the time to complete the task and therefore
reduce a worker's exposure. For example, although the bevelling
machine tested produced nearly twice the vibration level, it
completed the task in a tenth of the time.
For the grinding task it was found that the fibre disc and
rubber backing pad produced the lowest vibration and completed the
task in the quickest time. When the standard angle grinder was used
with anti-vibration handles, it was shown to consistently reduce
vibration regardless of the wheel used. The flap disc produced the
lowest noise; however, the operator commented that a flap disc is
not ideal for grinding off welds and instead would be used to
finish. The ceramic disc produced the lowest amount of dust.
The three bevelling machines produced lower noise, vibration,
dust and were more efficient than a standard angle grinder. The
bevelling machines also produced negligible amounts of dust due to
the nibbling action of the machine on the metal rather than a
grinding action.
For cutting using an angle grinder, the lowest vibration and
dust was produced using a diamond disc. However, this disc was
inefficient at completing the task and, in some cases, did not cut
the whole way through the rebar in the measurement period. The
lowest noise and the quickest was the carbon disc. An alternative
machine for cutting is a rebar cutter and this was shown to be
lowest in all emission categories. In addition, the rebar cutter
does not produce any dust due to its compression action, and the
operator commented that they could not feel any vibration through
the handles.
The Outcome
This work has shown that there are alternative machines and
wheels that can reduce vibration, noise and dust emission values
when compared to standard angle grinders and discs. However, it is
important that dutyholders take a holistic view and look at the
overall reductions that can be made. Alternatives to angle grinders
should be considered where possible.
In this application, HSE guidance is highly relevant: it is
important to identify efficient machines for the job, avoiding any
high noise or vibration models, and then manage the remaining noise
or vibration risk.
This work has enabled HSE to benchmark the performance of
products that claim to provide an advantage with regards to the
reduction of vibration, noise and dust, whilst providing
information on credible and practical methods for reducing
vibration, noise and dust exposures of grinder users.
In addition, this work has allowed promotion of effective angle
grinder controls to HSE Inspectors, and to the wider industry
through guidance drafted in collaboration with trade associations.
It is intended to directly link into enforcement activities and
advice.
For more information contact us by
email or using the enquiry
form.